摘要: 汽车产品开发的效率要让制造模拟产生最大的效用,必须使用关键叁数进行快速测试,以找出更隹、更可靠的设计解决方案。
时代变了,汽车被赋予的意义越来越充满智慧和未来感。如今控制一辆现代客车所需的程式码行数甚至可能比商用飞机和Facebook还多,而且这还没有将自动驾驶纳入考虑。这其中也许更重要的是设计和制造汽车所需的大量软体。典型的汽车专案需要数千名工程师使用CAD系统定义几何结构,使用物理模拟工具验证效能,然後才能建构任意实体原型,接着使用制造软体来最隹化工厂营运和供应链。
尽管有如此庞大的数位化基础设施,汽车产品开发的效率与汽车企业的期待仍然相去甚远。例如在完成设计阶段性目标後,汽车制造商平均要用数周的时间来建构精细的汽车模拟模型,接着还要用另外几周的时间来创建模拟和汇总相关模拟结果。这些延迟不仅影响汽车开发的整体用时,也妨碍设计探索与设计创新。
试想一下,如果在学习钢琴的时候,按下一个琴键,要等一个月才能听到所产生的音符,会是怎样的情况?这就相当於在使用模拟时,要看到产品的行为方式需要等待一个月。因此,要让模拟产生最大效用,必须使用关键叁数进行快速测试,以找出更隹、更可靠的设计解决方案。
毋庸置疑,汽车OEM厂商非常希??让设计团队和模拟团队更高效地展开协作。实际上,世界各地的电动车新创公司正在证明这种做法。在不使用数十年老旧工具和流程的情况下,借鉴软体工程的做法,组织更加敏捷的开发团队。??普遍采用3DEXPERIENCE平台实现传统开发环境下无法提供的协作模式和工作效率。
透过将3DEXPERIENCE平台与其设计模拟关联性和自动化网格、扣件和配置管理进行完美结合,能够将模拟模型的建构时间明显缩短多达五倍(图1),并且还将继续进行相关改善。
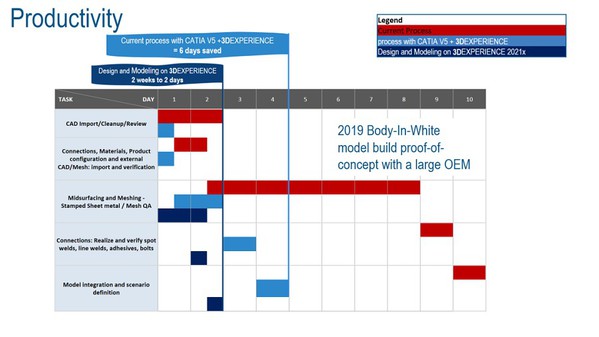
图1 : 白车身(Body-In-White)模拟建模时间加快 |
|
跨越隔阂,推动数位连续性与协作
以车身工程为重点,我们在图2中可以看到目前面临的一些挑战。首先,互不相连的工具链造成设计、工程与制造之间隔阂重重。以下是大多数OEM厂商的车身工程环境现状的典型示意图。
无法在设计与模拟间有效地维持模型可追溯性和连续性仍然是生产的一大障碍。3DEXPERIENCE平台可为所有结构属性都提供统一的主模型(图3),方便用户自动为碰撞、NVH和耐久性模拟衍生合适的模型,进而解决这个难题。
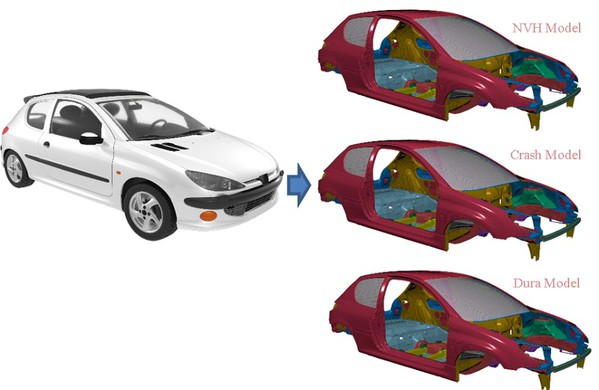
图3 : 从主设计模型我们能自动为不同效能属性产生模拟模型 |
|
3DEXPERIENCE平台能用CAD资料自动创建有限元网格。从同一个设计出发,您能够为各种类型的模拟管理不同网格密度和不同几何结构简化(删除倒圆角、忽略小孔等)的多种网格表现。这些网格与设计几何结构相互关联,所以可以在修改几何结构後更新模型,不必重新创建分析属性。还可以使用奠基於规则的批量网格划分技术,自动网格化由数百个壳体部件构成的大型装配。
典型的现代车身可能使用多达500个部件和5,000个扣件。後者的组成包括点焊、缝焊、铆钉、螺栓和黏合剂,如图5所示。
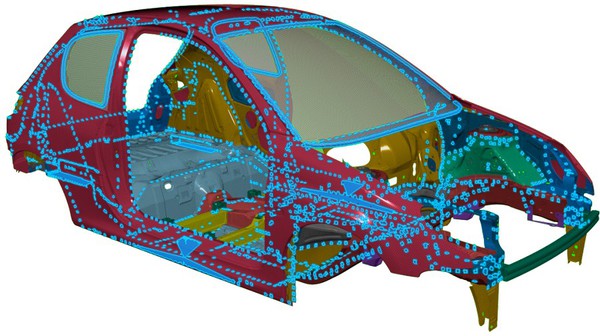
图5 : 图为典型汽车的扣件,例如点焊、缝焊、黏合剂、螺栓 |
|
为了以最低成本实现效能,OEM厂商极为关注对扣件的布局进行最隹化。但是由於设计、模拟和制造团队分别维持独立的扣件资讯库,团队间资料经常不同步或发生遗失。
此外,即便是在模拟部门内部,仍然需要为不同的效能属性管理多种扣件的表现。例如,NVH模拟中不需要针对点焊预测失效,但在碰撞模拟中就需要针对点焊预测失效。透过3DEXPERIENCE平台,也可以为不同属性管理多种扣件表现。
最後,同一车辆的多种配置可能需要针对同一需求展开多次模拟。3DEXPERIENCE平台能让使用者根据汽车配置轻松地筛选设计,然後自动产生合适的模拟模型。
需求驱动模拟
从根本上说,企业使用模拟的主因之一是预测产品效能对需求的符合度。物理测试的缺点不是成本过高,就是过於费时,或者两者兼具。随着汽车的复杂性不断增加,内部要求、消费者要求以及合规要求也随之增加。例如,以下的示意图展现过去50年中对碰撞安全需求的大幅增加。
3DEXPERIENCE平台能管理需求与模拟验证或物理测试验证间的反??环路。在整个开发过程中持续地将所有这些资讯都整合到统一平台上,提升以更快速度制定更优秀决策的可能性。
展开模拟的另一个主因是在开发中尽早地深入了解产品的行为和效能。透过使用模拟探索设计方案,能够快速剔除低劣设计,聚焦於最有发展性的方案,这就是为什麽要将快速设计探索的工具整合至3DEXPERIENCE平台的原因。
如今,在进行正式设计审核前,NVH、耐久性和碰撞团队不会展开协作。将资料统一在3DEXPEREINCE平台上,就能够持续不断地分享不同的设计方案和对策。透过这种方法,每个团队都能始终使用相同的资料,CAE团队也不必在上一个设计阶段通过後,需要等到下一个阶段才能验证彼此的方案。
这种跨职务协作自然地促进多学科最隹化。在当今的大多数OEM厂商中,资料与组织方面的重重隔阂,真正的多学科最隹化依然少见。3DEXPERIENCE平台不仅能促进前所未有的协作,也能为设计探索与最隹化提供紧密整合的用户体验。可以在定义模拟模型的时候,直接最隹化形状和大小叁数,如材料属性和测量厚度等。
总之,多个团队用多种互不相连的工具展开工作的传统方式,将难以在下一轮创新浪潮和竞争压力下生存。3DEXPERIENCE平台可为解决这些挑战提供下列主要价值:
* 为设计、模拟和制造提供统一的主模型
* 自动化的CAD关联模拟模型建构方法可提供数位连续性,快速解决设计变更和汽车变型问题
* 为不同属性的模拟提供一体化的扣件管理和网格管理
* 针对设计探索和多学科最隹化的协同工程
* 透过仪表板展开需求驱动的模拟
随着企业扩大对汽车电气化和自动驾驶、碰撞、耐久性和NVH的投资,各部门需要在节省资源的同时提高生产力。尽管具备出色的结构效能极为必要,但还不够。现在面临的挑战是在以最低成本满足所有结构属性的前提下实现优异的效能。达梭系统正在与其客户共同努力,以支援这些重要转型。
(本文作者Katie Corey为达梭系统SIMULIA内容创作者;Deepak Goyal为SIMULIA航空航太与国防工业成长团队模拟顾问)