纯电动汽车(BEV)有严重的重量问题,但这种问题 Weight Watchers 无法解决。
许多纯电动汽车比内燃机汽车(ICE)重33%。美国国家运输安全委员会主席指出:「福特 F-150 Lightning比非电动版本重2000到3000磅。」另外,美国国家经济研究局(National Bureau of Economic Research)发现,车辆每增加 1,000 磅,事故死亡风险就会增加约 47%。
因此,汽车 OEM 厂商在尝试设计续航里程更长、安全性更高和电子内容更多的纯电动汽车时,面临严峻的限制条件。这是该产业有史以来面临的最严峻研发挑战之一。
尽管面临巨大的挑战,但如果电动汽车中的传统超重供电网路(PDN)被 48V 区域架构取代,其中48V母线取代原有 12V 系统,则可减少 OEM 厂商、消费者和立法者的这些担??。部署由高密度电源模组支援的区域架构,将以3种方式减轻重量。这种新架构将实现从粗线束到细线束的过渡,可将线束重量减少 85%。此外,低压辅助电池可拆除并使用电源模组进行虚拟化,从而可完全消除电池重量。最後,使用电源模组进行PDN升级,可最隹化热管理系统,从而将其重量减少 33%。
因此,采用分散式架构替代传统集中式架构,可显着减轻重量,还可提高整体电力系统效率。
对於纯电动汽车而言,采用 48V是期盼已久的明显改进
在每个设计周期,新车都会增加安全、保全和自动驾驶等新电子产品。每个额外的功能都会增加功耗,使用固定标准化电池已转化为电流的指数级成长。从电流趋势来看(图一),集中式架构 PDN 是不可持续的。要恢复可持续电流位准并最大限度减少线束重量的同时,满足不断成长的电力需求,唯一的方法就是使用区域架构将工作电压提高至 48V。

图一 : 转换为 48V 系统,会将车辆总电流从 250A 以上降至 75A 以下,不会影响车辆电气效能。 |
|
自 1908 年以来,随着汽车电子设备的增加,汽车电流需求已呈指数级成长。20 世纪 60 年代,OEM 厂商将电压从 6V 提高到 12V,导致电流在 60 年首次减少。尽管现在需要更大的电流,但大多数 OEM 厂商仍然使用 12V 母线。2023 年,特斯拉成为首家宣布在整个汽车中全面采用 48V 母线的 OEM 厂商,这将大大降低电流需求。
目前的纯电动汽车由主高压电池(通常为 400V 或 800V)供电,不仅需要为电动牵引马达供电,而且还需要为大量低压负载供电,如空调、加热座椅和资讯娱乐系统等。PDN会将高压降至48V及12V辅助电池电压,为这些子系统供电。
根据欧姆定律,转而采用48V分散式架构将带来一个机会:功率=电流x 电压
功率输出相同时,12V电源需要的电流是 48V 电源的四倍。因此,12V导线一般也比48V导线粗四倍。
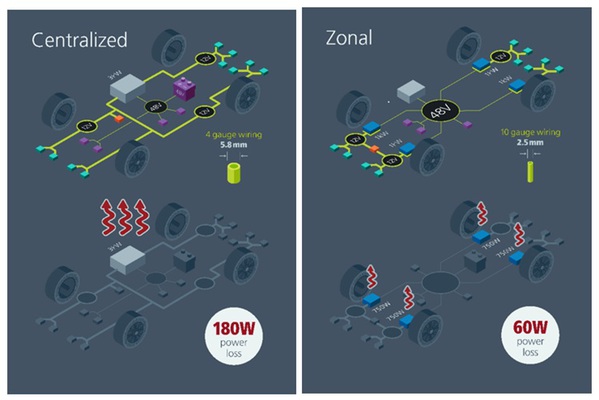
图二 : 当今汽车有两种不同的 PDN:12V 集中式架构和快速发展的48V分散式架构。前者采用12V粗线束,後者采用 48V 细线束,细线束重量更轻,减少了热损耗,而且将电流降至 1/4。 |
|
终结12V 集中式架构
自20世纪60年代以来,12V集中式系统一直是汽车使用的传统电源架构。该架构由一个庞大的银盒外壳组成,其中包含一系列分立式元件,例如所有将高压(HV)转换成48V至12V的 DC-DC转换器等。这个系统需要使用粗重的导线将12V电流传输至负载点。此外,由於传统的 DC-DC转换效率低,这种集中式电源系统会从银盒产生大量热量,通常需要密集的液冷,这会增加更多的重量。
要过渡到48V,可在端点位置使用高密度电源模组,以便在负载点高效转换为12V。这使OEM厂商能够随着时间的推移,高度灵活地逐渐将12V负载器件过渡到48V。这有助於在对系统架构干扰最小的情况下,快速实现使用 48V的优势。
48V分散式架构降低热损耗、减少电流
新颖的48V分散式架构系统利用欧姆定律,其中DC-DC转换发生在更靠近负载点的位置,而不是在中央银盒(Silver Box)内完成。在该方案中,高压至48V的转换有助於将安全的48V用作整个车辆的母线电压。48V至12V的转换在负载点位置进行。透过 48V 而非 12V 传输电流,导线可以更细、更轻,很明显,成本也会更低(图二)。这种更细、更灵活的导线也更容易在车内布局。此外,这种方法可将与DC-DC转换器有关的热损耗均匀地分布在整个车上,从而可使用安装在底盘上的热传导及空气对流散热系统的潜能。
检视减少的重量
48V分散式架构不仅可更加支援纯电动汽车日益成长的动力需求,同时还可采用 3 种方法减轻汽车重量。
1.线束:重量锐减约 85%
升级到48V分区架构,意味着传统的273克/公尺的12V、4号电线将被27克/公尺的48V、10 号电线取代。这可减轻大约 85% 的导线重量。
2.辅助蓄电池取消:重量减少~100%
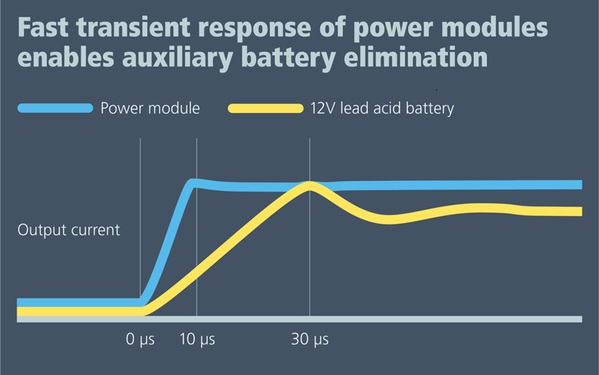
图三 : 电源模组可实现比 12V 铅酸电池更快的暂态响应,从而建立虚拟电池,可取代传统的笨重 12V 电池。 |
|
电源模组的分散式架构可加速 DC-DC 转换器的暂态响应,从而建立虚拟电池。因此,12V/48V分散式电源模组不仅可复制 12/48V 低压电池的特徵,同时完全消除了实体 12V 电池,减轻了100%的重量。
3.电源系统最隹化:重量减轻约 33%
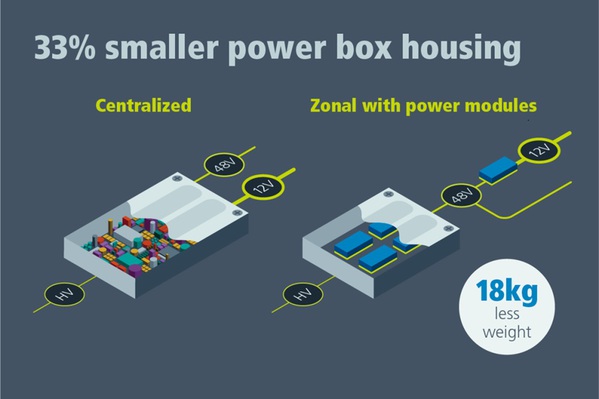
图四 : 使用电源模组和分散式架构时,可缩小集中式外壳,因为在 48V 转换为 12V 负载的端点可以更有效率地散热。 |
|
用区域系统取代集中式系统,可将48V至12V电源转换从银盒移至负载点。改进後采用高密度电源模组提供48V输出的电源系统盒将缩小达33%。因此,外壳重量可减轻多达三分之一 (33%)。
在传统12V集中式系统中,分立式元件会在其银盒外壳内产生环境高温。采用高密度电源模组的电源系统盒产生的热量较少,而且负载点模组可在底盘上进行高效的通风散热。这些改进可使液冷系统瘦身 7%。
OEM厂商可使用分散式架构获得各种优势。请考虑减轻重量对增加行驶里程的影响。当车辆越重,能耗就越大,行驶里程也就越短。然而如果将其用来增加电池尺寸,额外的重量就可降低对续航里程的影响。额外的电池提供更多的能量储存,可增加续航里程。
在Vicor的研究之一,高密度电源模组支援的分布架构可将车辆重量减轻40磅。在该重量被 40 磅的电池所取代时,在不增加净重的情况下,电动汽车的行驶里程每年可增加4000英里。这一点非常重要,根据美国联邦公路管理局2023年的资料显示,美国人平均每年开车的行驶里程为 14,263 英里。因此,使用48V分散式架构可减少每年30%的充电时间,并增加车辆一次充电的行驶里程。
以创新消除重量疑虑
电动汽车超重,这种趋势既不能持续,也不利於电动汽车的整体发展。采用传统银盒和分立式元件的 12V 集中式架构需要升级到 48V 分散式架构,以最隹化电动汽车的供电网路和散热管理系统。分散式架构可将每年的行驶里程增加 4000 英里,也可用於实现额外的安全或电子功能。
最高效的区域架构在负载点使用小型轻量级转换器。高效的高功率密度模组是 48V 至 12V 转换的最隹选择。鉴於目前复杂的汽车电力电子产品,OEM厂商不仅需要创造性地减轻重量,同时还需要提高效能。此外,小巧精巧的电源模组也是 48V 区域架构显而易见的选择及合理补充,48V 区域架构是汽车产业供电网路的未来。
(本文作者Noa Margolin为Vicor 公司研发工程师)